ASEA Goes Home Early Thanks to ReadyShipper X’s Breakneck Speeds & Uptime
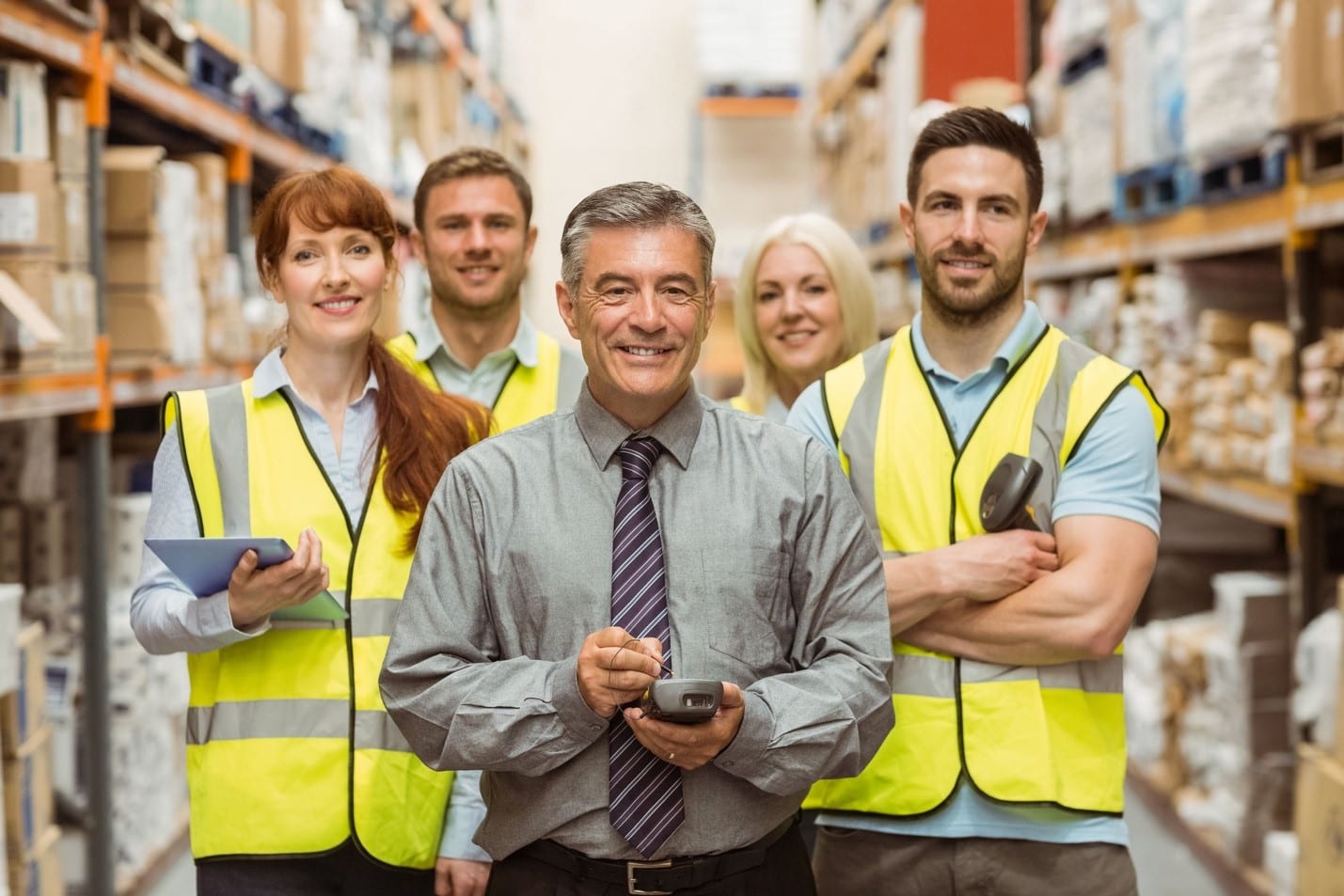
ASEA, a provider of popular organic products, was plagued by inadequate fulfillment and slow packing speeds. ReadyShipper X came to the rescue so everyone could go home early.
We had a chance to sit down with the head of the Fulfillment Department at ASEA to ask them what they thought about ReadyShipper X after switching to our system. Here’s the scoop.
Q: What were your Pain Points like before using ReadyShipper?
Eli: Well, I was one of the ones who recommended ReadyShipper to the team.
The user-friendliness of this program compared to what we used to use is night and day. Being able to manipulate your own boxes, batch print, and the customer support that you offer all stand out. Knowing that we can reach out to you guys is the biggest difference between or current and our older system.
Q: What’s your favorite feature of RSX?
Jose: Being able to batch print and control that… with options for splitting boxes or using multiple boxes. The way that the API communicates makes a big difference. Additionally, this gives a better way to control our product more without having to rely on a 3PL.
Q: What would you say is the best part about using RSX as compared to your old shipping software?
Jose: From my point of view, I’ve seen different software before, and being involved in the direct selling industry, the biggest selling point for RSX, in my opinion, is ease-of-use. It’s very user-friendly!
CASE STUDY
ASEA was facing a number of hurdles they wanted to overcome to make their fulfillment department more efficient. Due to inefficiences, workers were staying late, the pick and pack process was sluggish and everyone was working overtime.
Too many touchpoints. ASEA had a variety of necessary manual actions that were required with each package, such as secondary scanning of invoices during the packing process.
RSX Solution: ReadyShipper X eliminated these touch points, helping ASEA fulfill packages at three times the speed. The result: 300% increase in fulfillment efficiency from day one.
Sluggish label printing speeds. ASEA’s previous shipping software program was a browser-based program that was reliant on internet speed, uptime and loading.
RSX Solution: Once ReadyShipper X’s thin, hybrid-cloud client was in place, they were able to eliminate browser lag and increase label printing speeds to 3 per second. The result: 300% increase in label printing efficiency with eradication of tedious manual functions and uncessary touchpoints.
Poor routing and networking. ASEA’s previous system wasn’t efficient. It didn’t route or network to the nodes properly and required a lot of manual work during the process. This often resulted in longer work hours with the managers ordering pizza frequently to charge up overworked employees who were staying late.
RSX Solution: Now, the entire staff goes home early with fulfillment accuracy increases, fewer manual touchpoints, a greatly improved packing process and nodes that can be networked and assigned throughout the warehouse for greater efficiency.
Non user-friendly system. ASEA’s previous system wasn’t very user-friendly, it had a lot of confusing features and functions and too many pain points to optimize their fulfillment process.
RSX Solution: ReadyShipper X’s user-friendly and intuitive interface helped ASEA’s employees dive right into a new system with ease. The automation processes and integrated functions help them batch print faster, organize shipments and orders, split boxes and choose the carrier of their choice.
No there’s no more late-night pizza for the hard workers at ASEA! All the packages are now shipped in a timely manner. Even better? Everybody goes home early!
Share On: